PRODUCT INFORMATION
ECO2Brew is unique in its design to recover CO2 from fermentation processes at larger 24/7 operating breweries (> 2,000,000 hl/yr).
BE CO2 SELF-SUFFICIENT
ECO2Brew is unique in its design to recover CO2 from fermentation processes at larger 24/7 operating breweries (> 2,000,000 hl/yr). Its 100 % water-free operation can save up to 1 m3 of water per tonne liquid CO2 in tank.
The purity of the liquid CO2 end product exceeds general quality standards for food/beverage/ingredient purposes including the latest edition of the ISBT standard.
Safety first! Since our system utilizes the brewer’s glycol to liquefy the CO2 the operation is free of Freon or Ammonia!
Our plug-and-play ECO2Brew comes pre-packaged with all parts mounted pre-wired and pre-piped on two 40 ft skids and allows for fast and easy installation. A containerized solution for outside mounting is optional. At the heart of the ECO2Brew sits a proprietary technology: CO2Scrub. It has proven its worth purifying gas from bioethanol sources and is now successfully applied in the brewing industry. All this without any water consumption.
Are you wondering about the recovery rates? Especially at a lower feed gas purity recovery rates are significantly higher than what you’d obtain with traditional competitive technology, offering the possibility to recover excess CO2 for onsite soft drink production and/or export purposes.
Recovering your own CO2 lowers your site’s CO2 footprint and reduces your VOC emissions to the atmosphere. Both contribute to a more sustainable operation.
Our dedication to your CO2 self-sufficiency continues after the commissioning. Through comprehensive lifecycle management, our technical support and service team ensures that your ECO2Brew operates optimally.
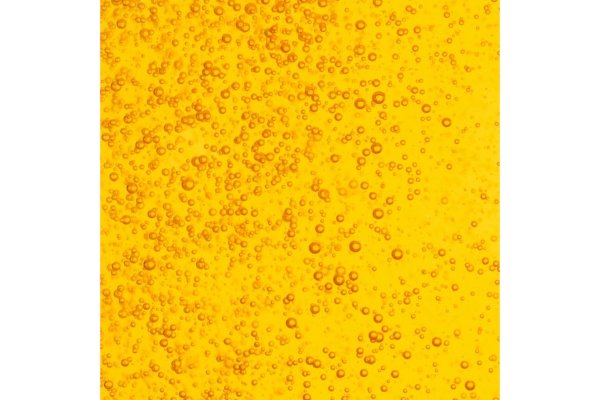
Benefits
- CO2 self-sufficiency and beyond
- High quality liquid CO2 ≥ 99.998 % v/v, O2 ≤ 5ppm v/v
- High recovery efficiency even at low CO2 inlet purity ≥ 90 % v/v
- Robust design for reliable 24/7 operation, uptime ≥ 95 %
- Low footprint (2x 40 ft skids)
- Pre-packaged plug-and-play solution
- Refrigerant free
- Up to 40 % energy savings with Glycol heated vaporizer
- Tolerant to gas from fermentation processes with high level of adjuncts (abnormal impurities)
-
PROCESS DESCRIPTION
-
Raw foam-free fermentation gas is fed to the ECO2Brew system where CO2 screw compressor units (1) increase the gas pressure to 48barg (696psig) in 3 stages removing condensate in the process. H2S is filtered after the 2nd stage. The remainder of the impurities is absorbed by liquid CO2 in the specially designed CO2Scrub (2), and purged into the atmosphere. The water in the gas is removed in the on-line drier (3) downstream. Regeneration of the off-line drier is automatic utilizing heating elements and dry CO2 purge gas. CO2 liquefaction takes place in the glycol cooled condenser (5), and O2 removed in the stripper (4). The flash gas is led back to the 2nd stage of the CO2 compressor, whilst the purified liquid CO2 end product is fed at 15 barg (218 psig) to the onsite storage tank.
-
OPTIONS
-
- Foam separator
- Gas booster
- Gas balloon, gas washer, and dry running 3-stage compressor (alternative to screw compressors)
- Liquid CO2 storage tank
- Ambient or Glycol heated vaporizer
- Cylinder filling unit
- Road tanker pump
- Quality control equipment
- Installation and commissioning services
- Original spare parts
- After-sales services
- Foam separator
Downloads
TITLE | DOWNLOAD PDF | |
Product leaflet | CO2 Recovery Plant - Haffmans ECO2Brew | Download |
Product leaflet | CO2 Recovery Plant - Haffmans ECO2Brew (German) | Download |
Case study | Lion Brewery | Download |
Technical documentation | Looking for operating instructions, installation manual, spare part list etc.? | Please, send us your request |
Related products
HAFFMANS CO2 RECOVERY PLANT - CO2MPACTBREW
CO2mpactBrew is a CO2 recovery plant especially designed for smaller, craft-sized breweries with capacity 50.000-350.000 hl/yr.
HAFFMANS CO2 RECOVERY - SYSTEM ENERGY SCAN
Scan your CO2 Recovery Systems with Haffmans and get detailed information on energy consumption, performance and quality.
HAFFMANS CO2 RECOVERY PLANT - CRU
Robust and reliable CO2 recovery solution for a wide variety of brewery needs ranging from 300,000 to beyond 5,000,000 hl/yr.